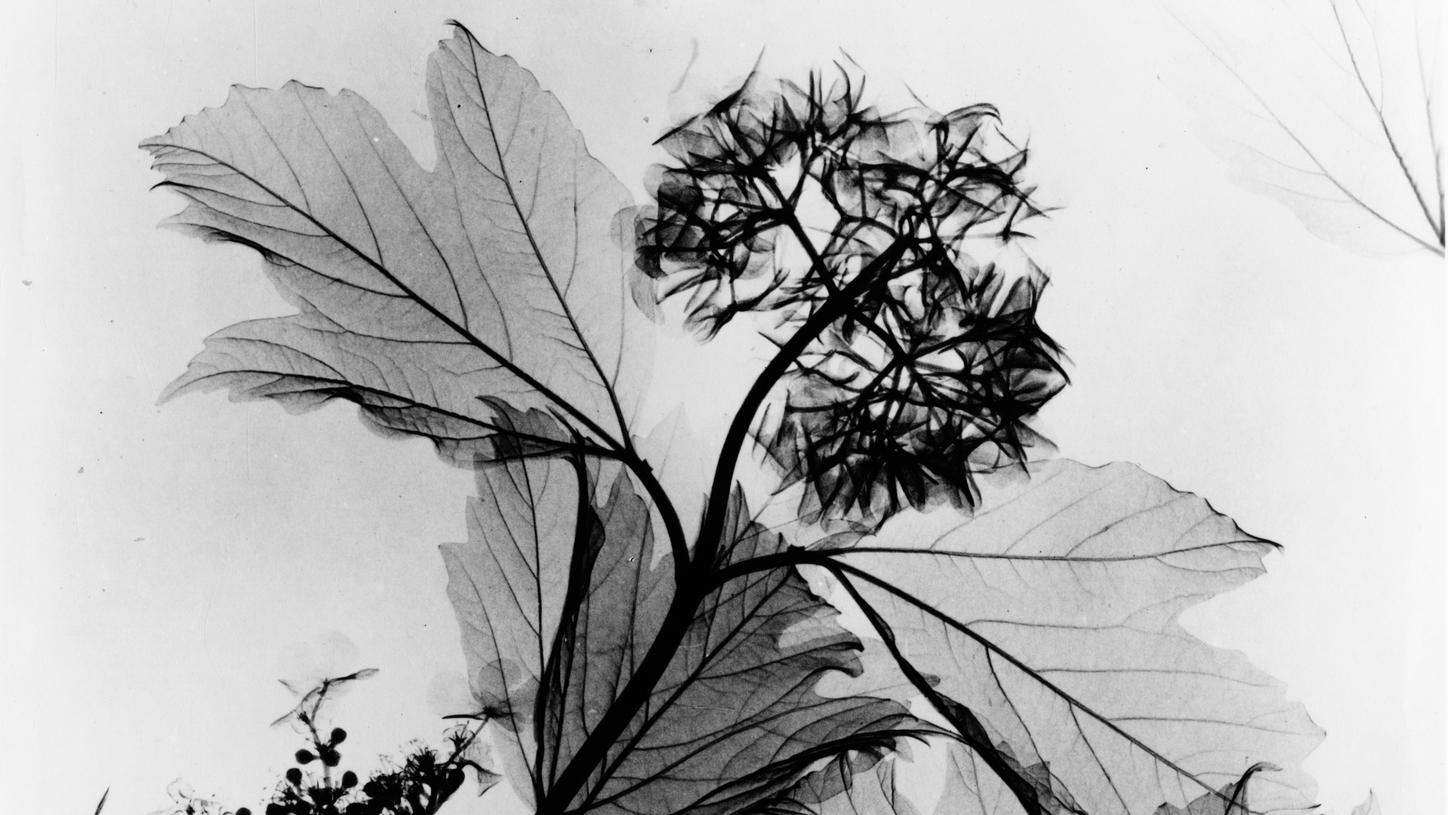
Planning for the future in the past
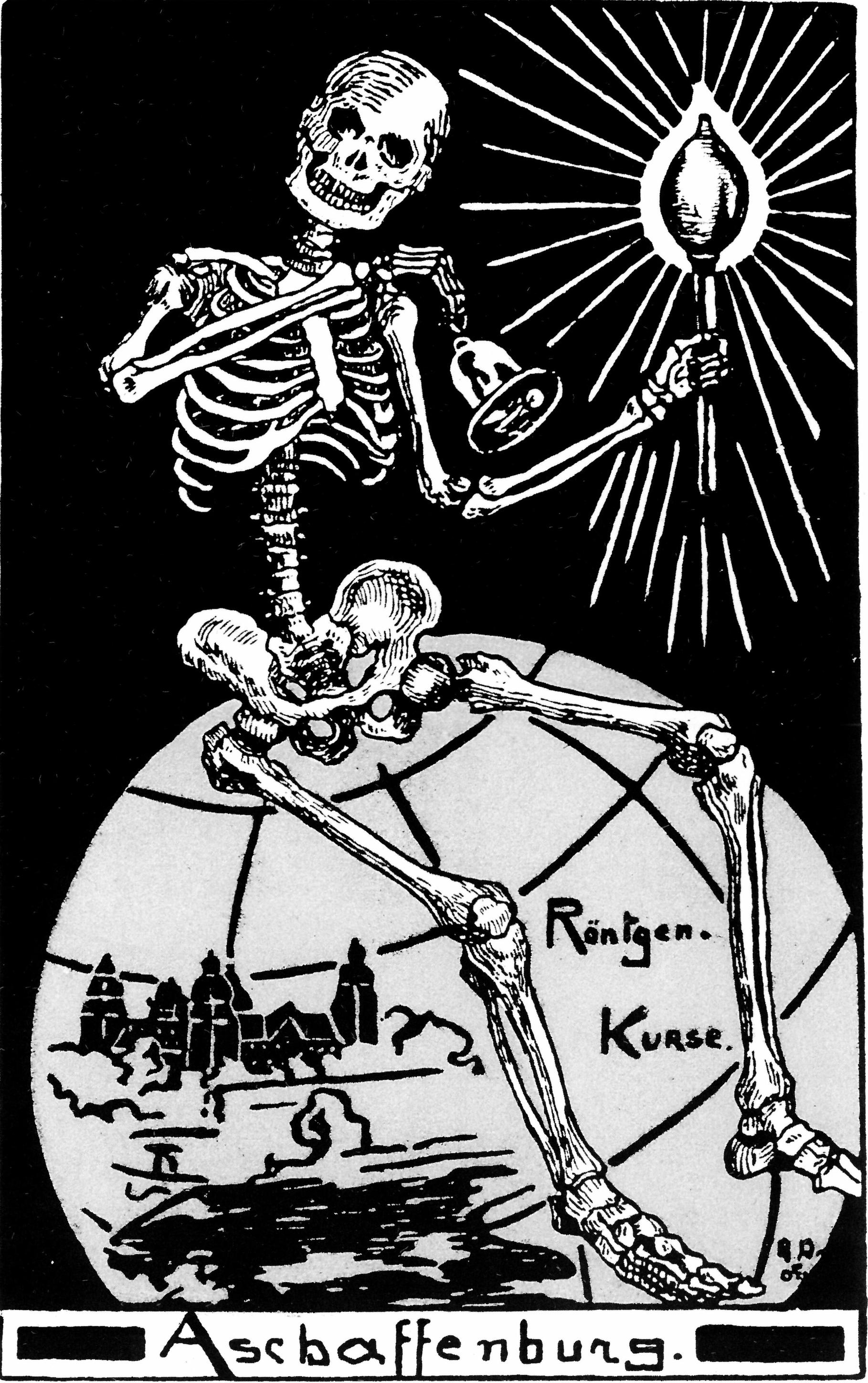
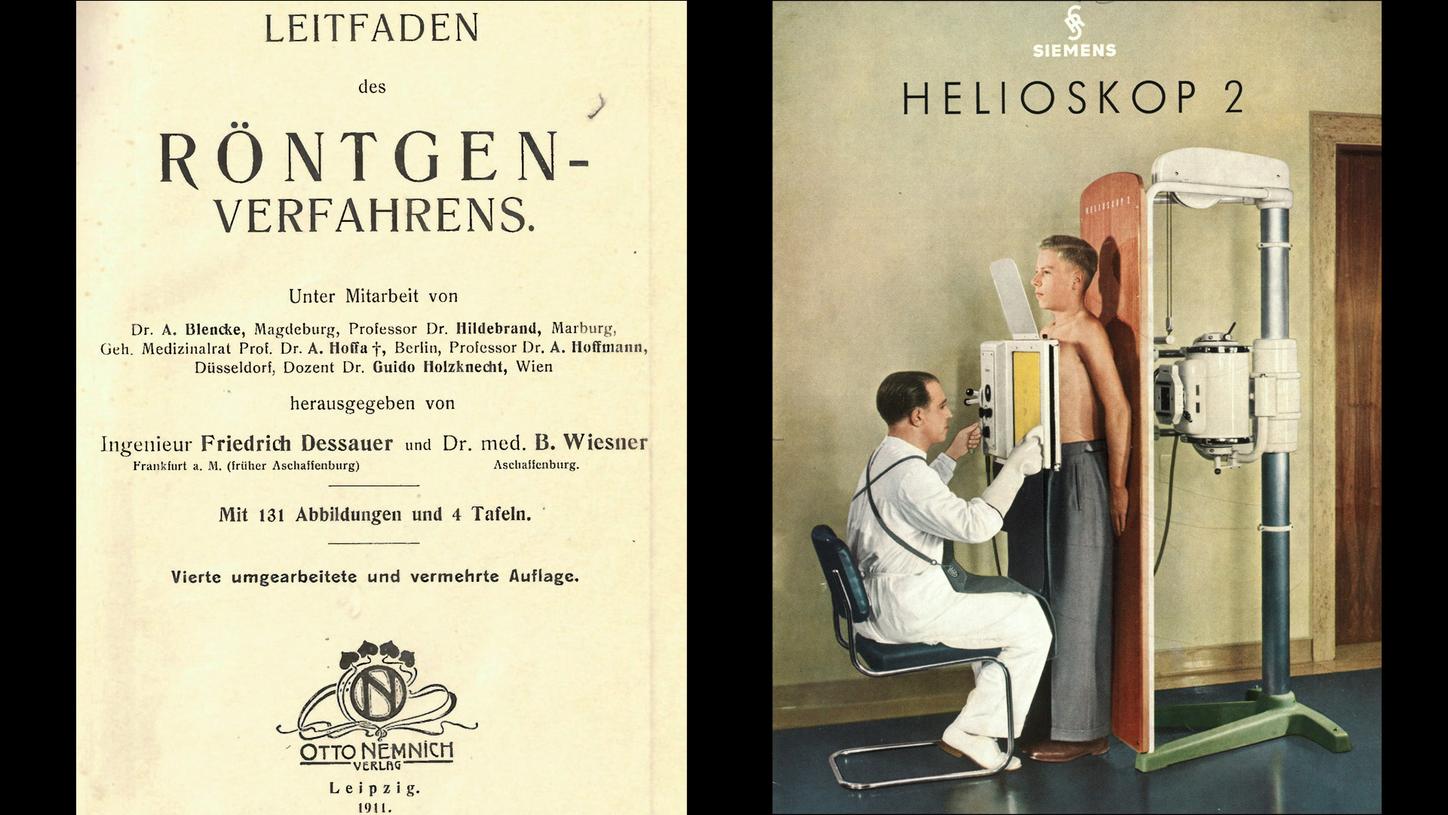
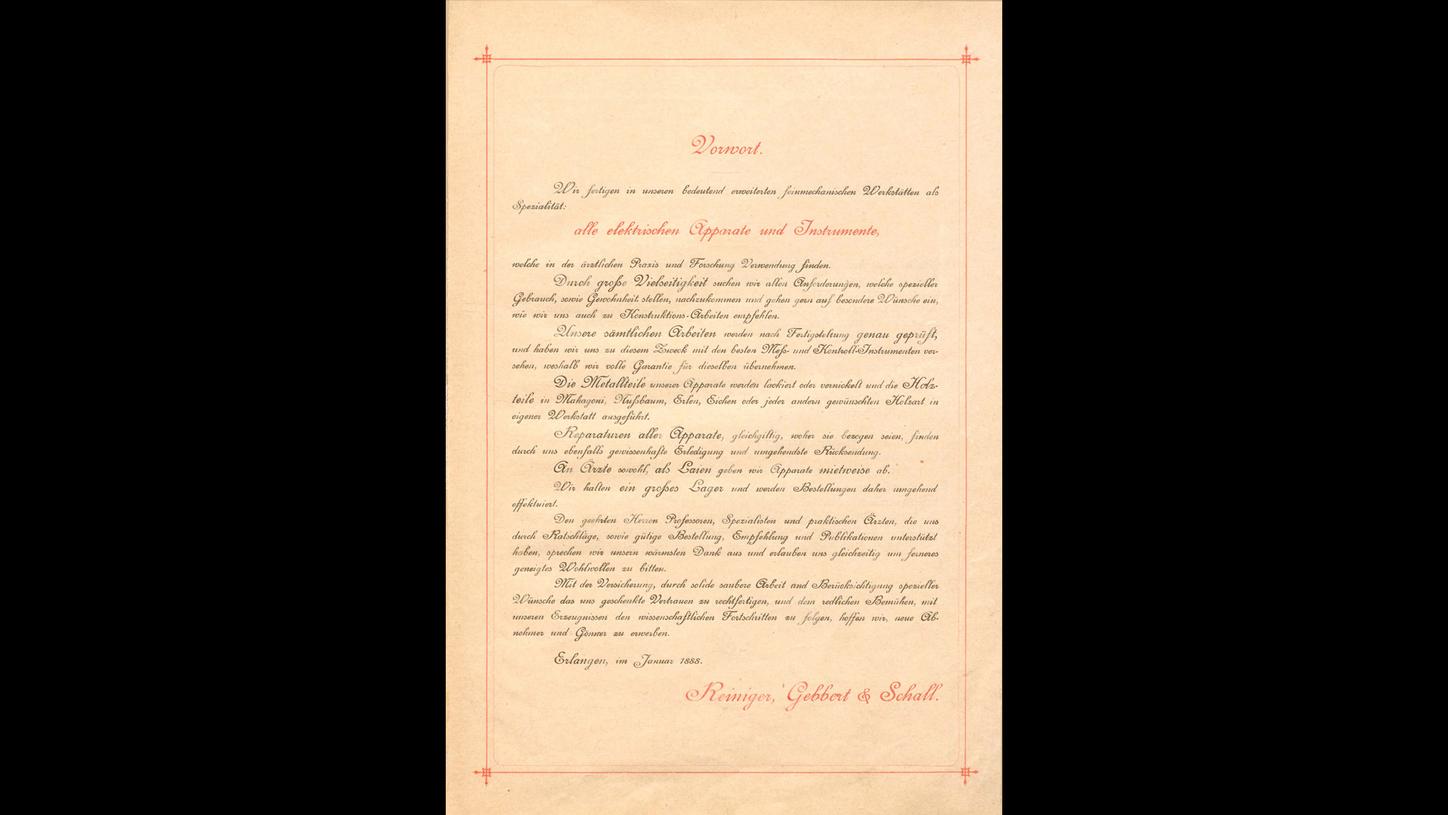
“We shall most gladly send apparatus and instruments to physicians for inspection and for leasing to their patients.”
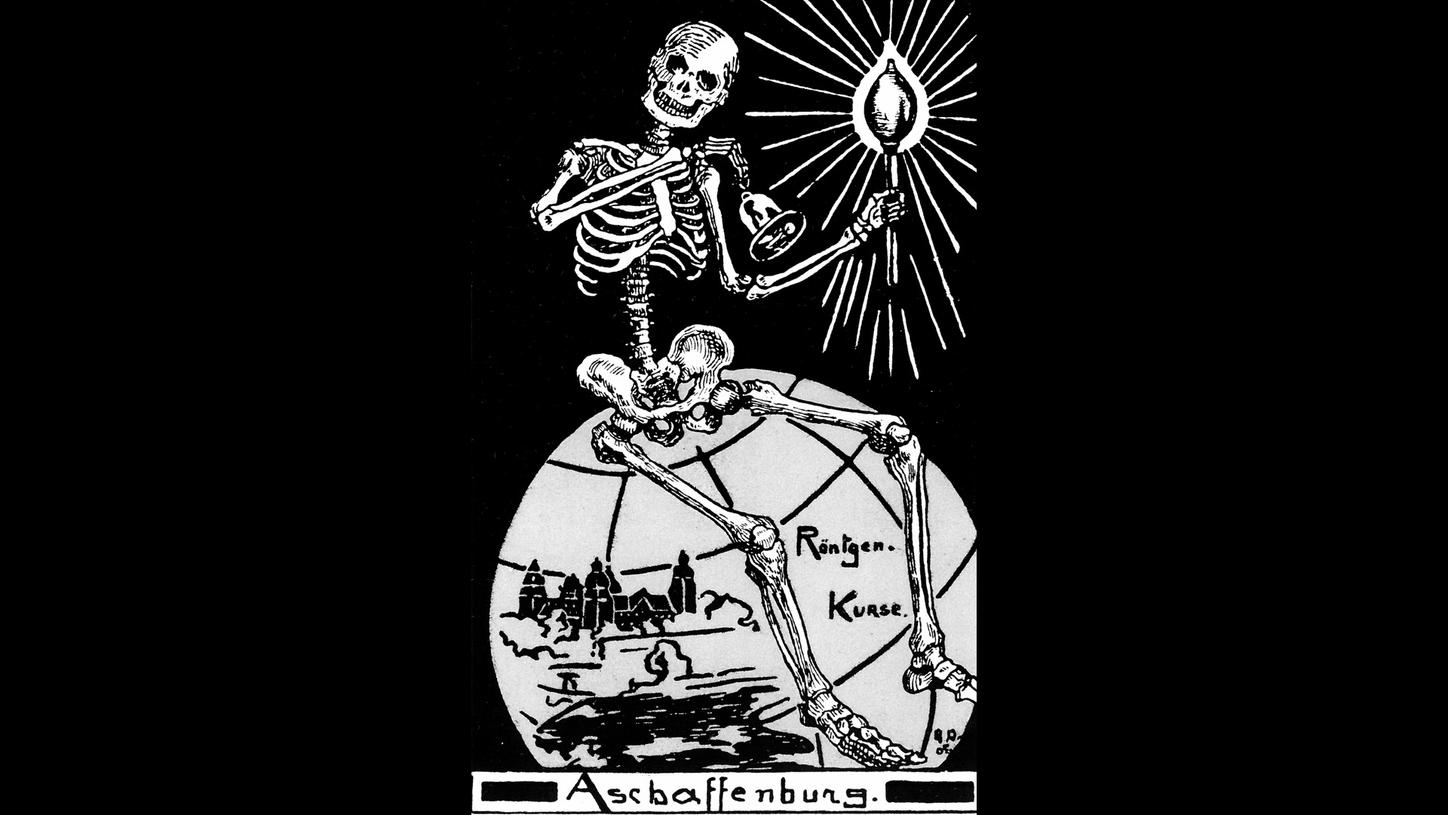
In addition, a lack of space and a shortage of staff in practices and clinics have always been obstacles to purchasing imaging systems. To enable as many people as possible to be examined using X-ray technology, Friedrich Dessauer began offering the ELA device, a compact X-ray system specially designed for smaller family practices, as far back as 1902. Over time, numerous devices (such as the X-ray Sphere from 1934 and the Helioskop from the 1950s) were developed that helped X-ray technology find its way into smaller medical practices. As well as being compact and affordable, these X-ray systems were also versatile, easy to use, and robust.
The MAGNETOM Free.Star turnkey solution
Diagnostics on wheels
Whether in a bus, in a truck, or on a ship, our imaging systems have long been used in mobile examination rooms. This has allowed them to reach people all over the world and improve medical care even in remote and poorly served regions.
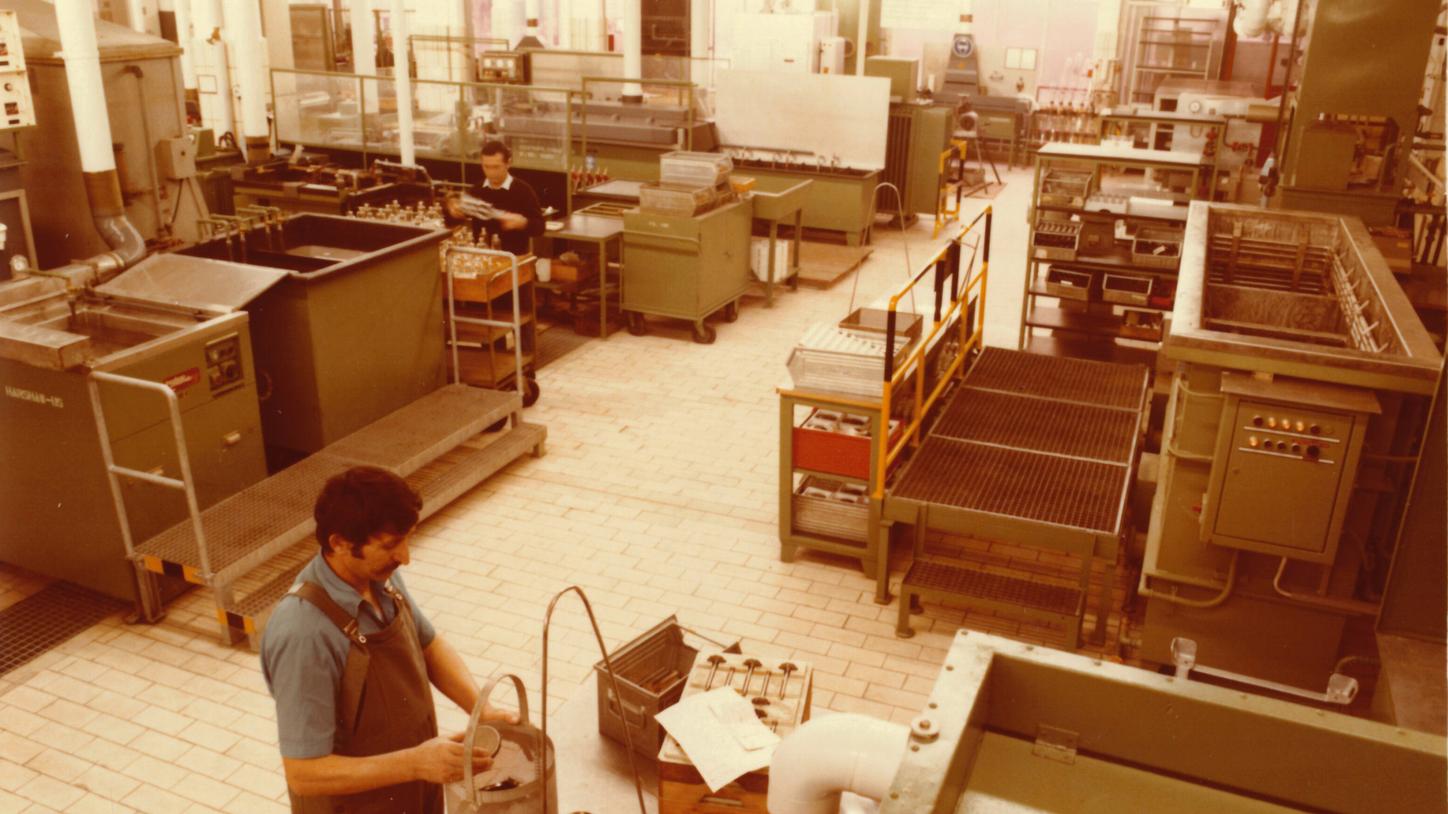
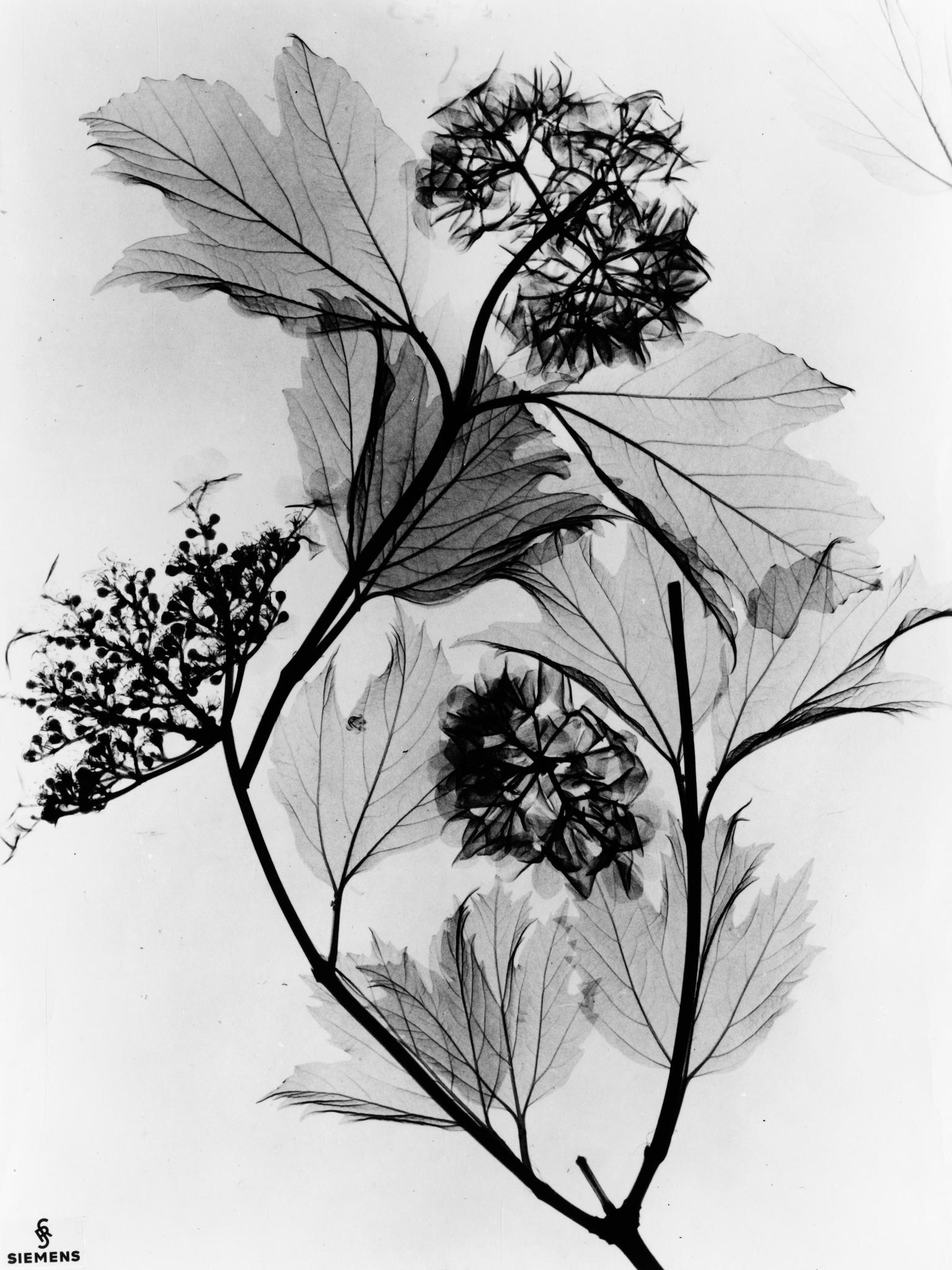
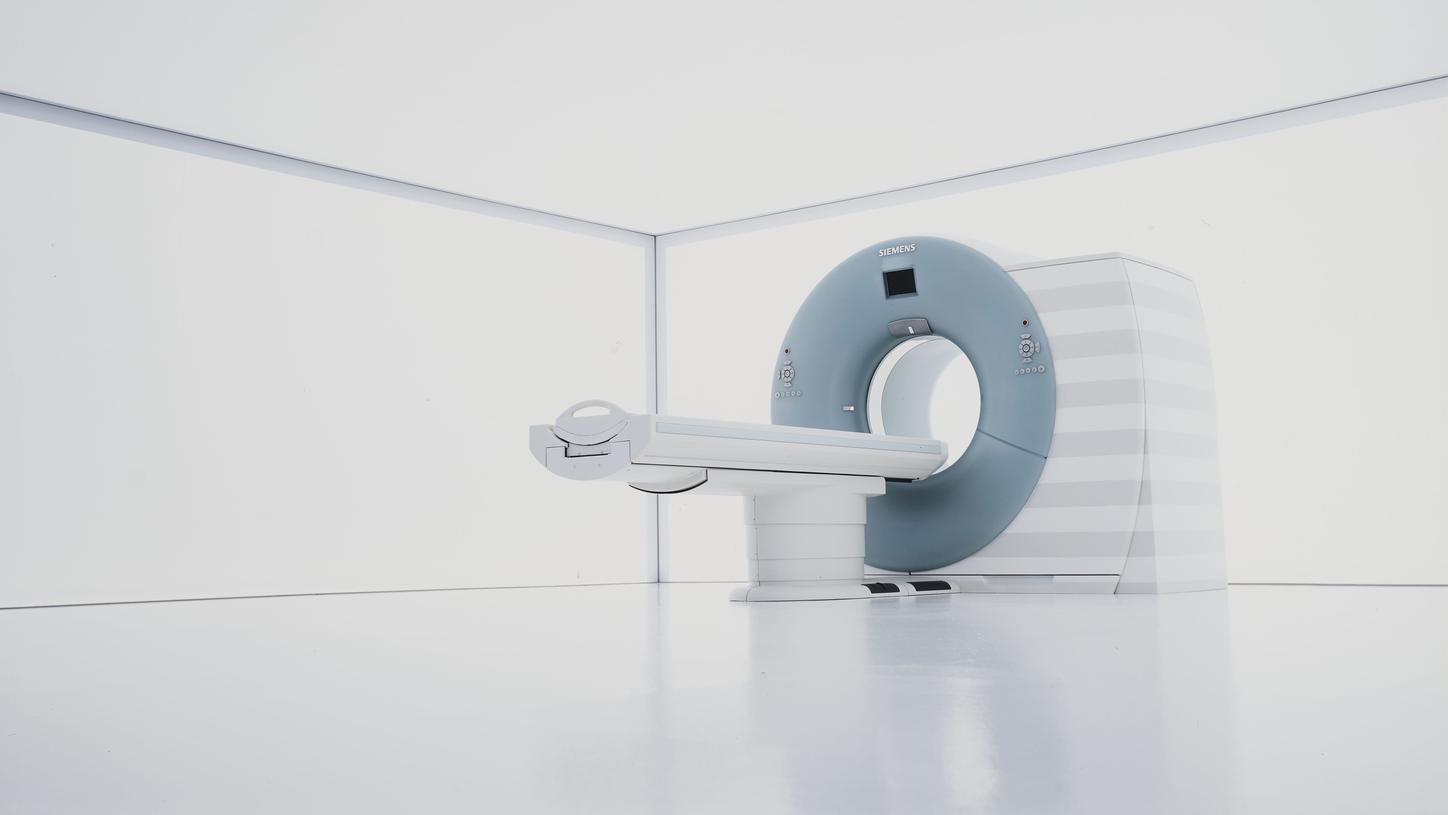
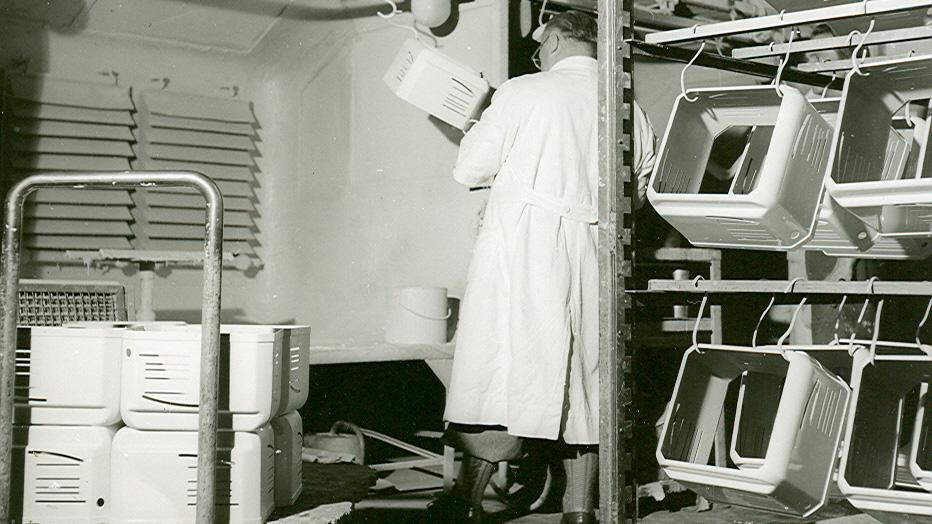
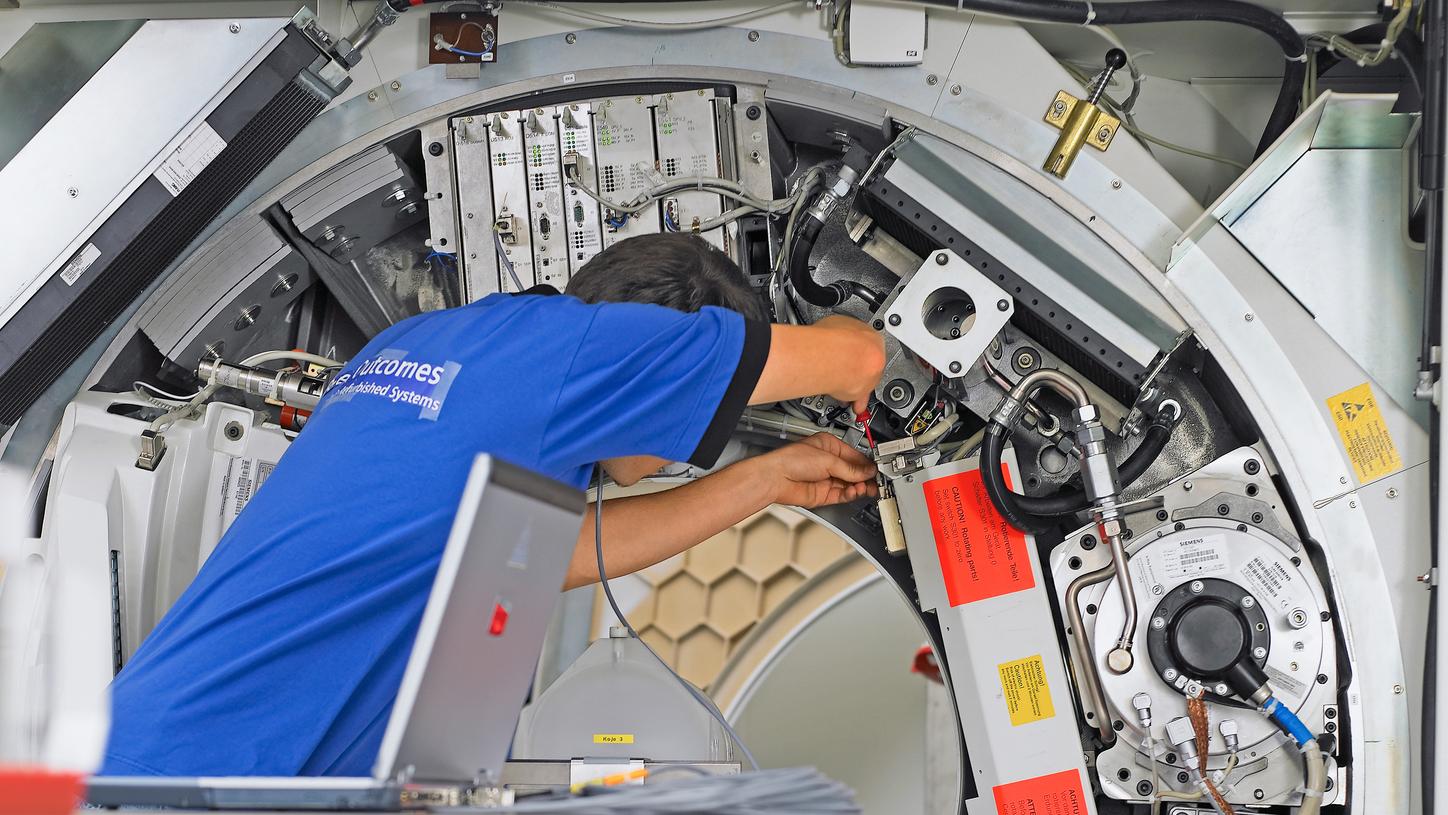
Older devices that cannot be refurbished can be used for spare parts or be disposed of in an environmentally friendly way. Experience gained from recycling and disposing of devices flows directly into the development of new devices so that they are easier to recycle. As early as 1993, Siemens became the first major European company to introduce an internal standard that required products to be optimized in terms of their environmental compatibility during the development phase. This included designing them for efficient consumption, avoiding the use of hazardous materials, minimizing the number of different materials used, and enabling good recyclability.
Electroplating at the Erlangen factory, 1952
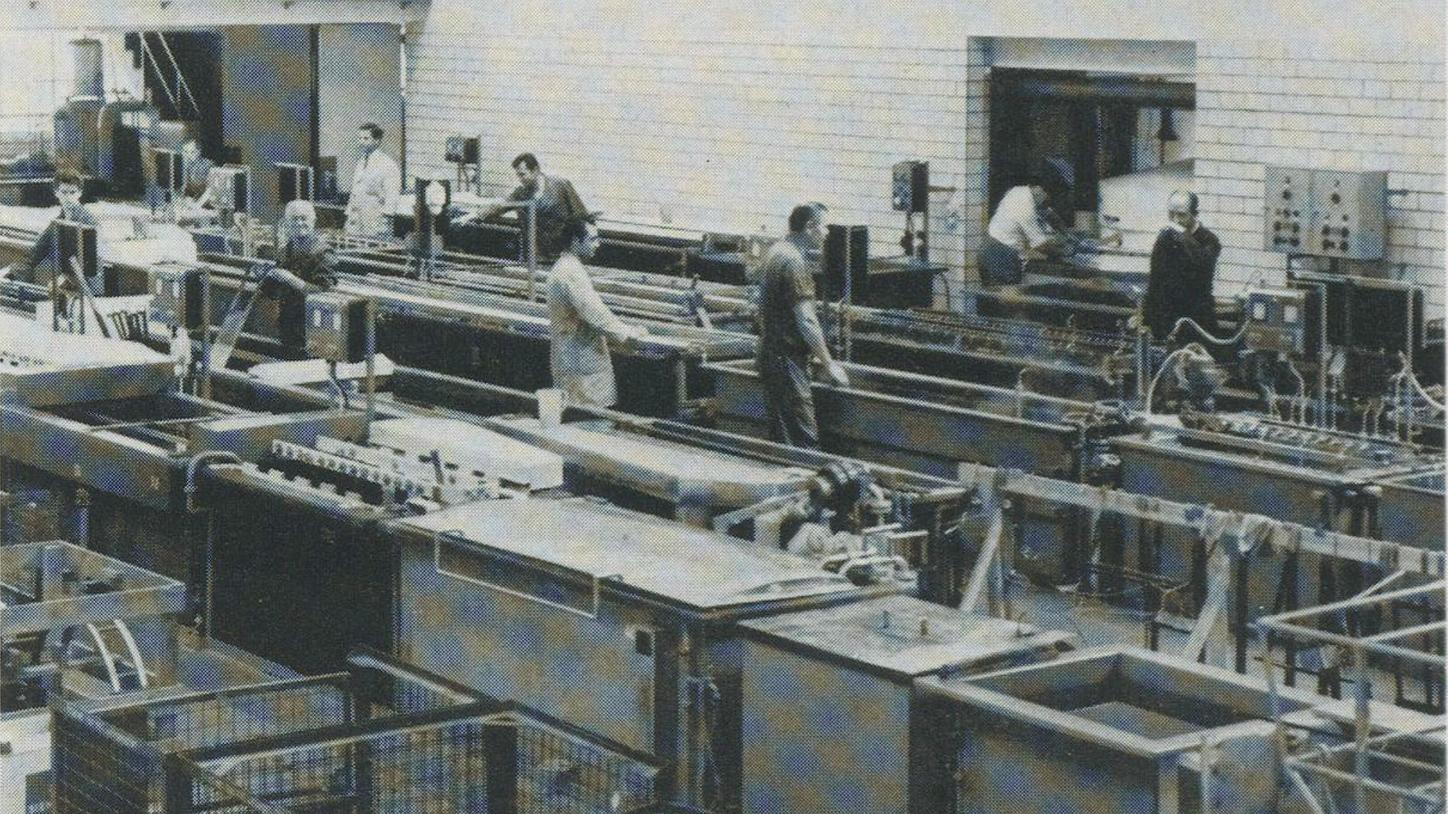
Baths at the new electroplating workshop, 1967

The new electroplating equipment at the tube factory in Rudolstadt, 1993
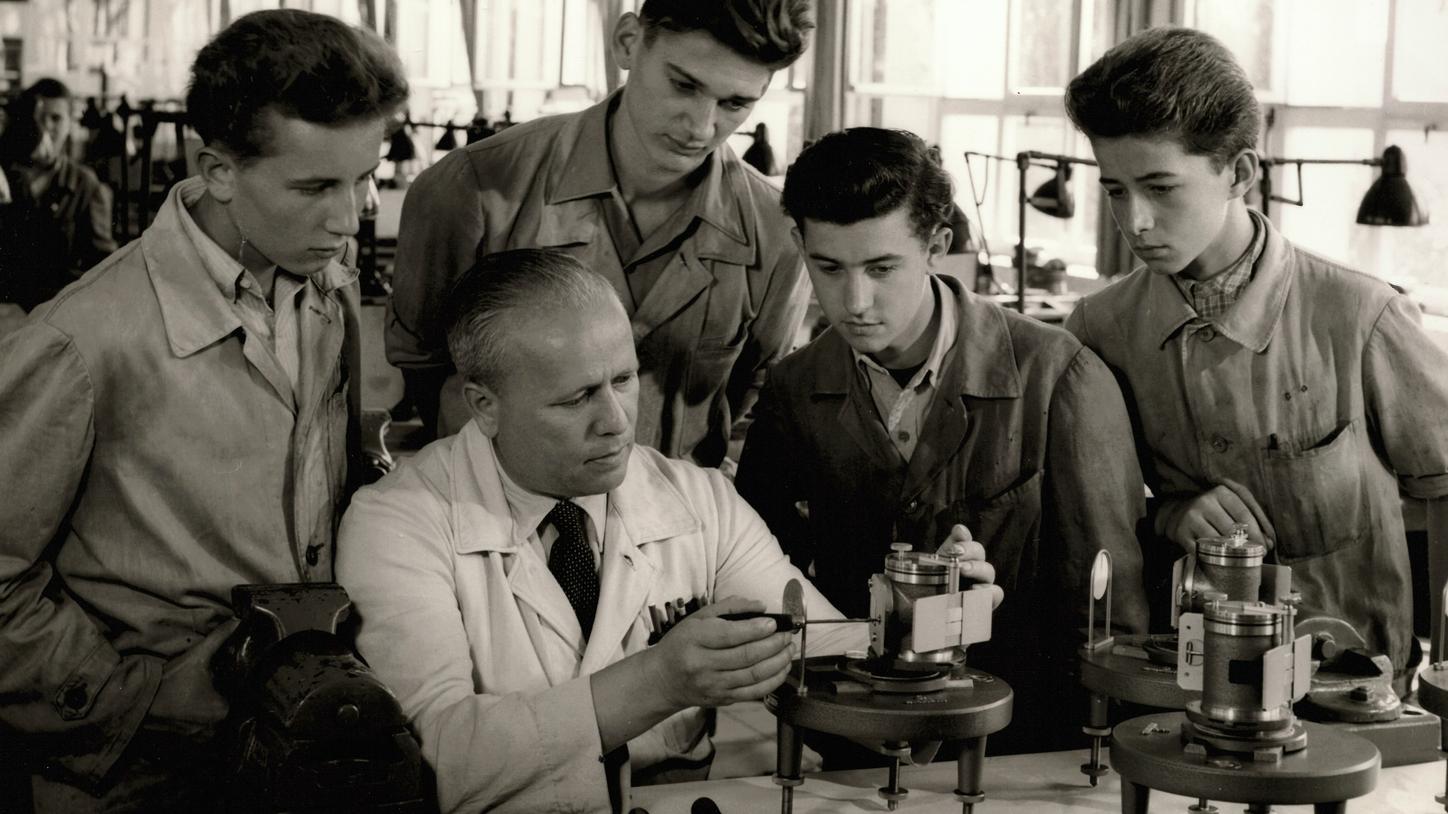
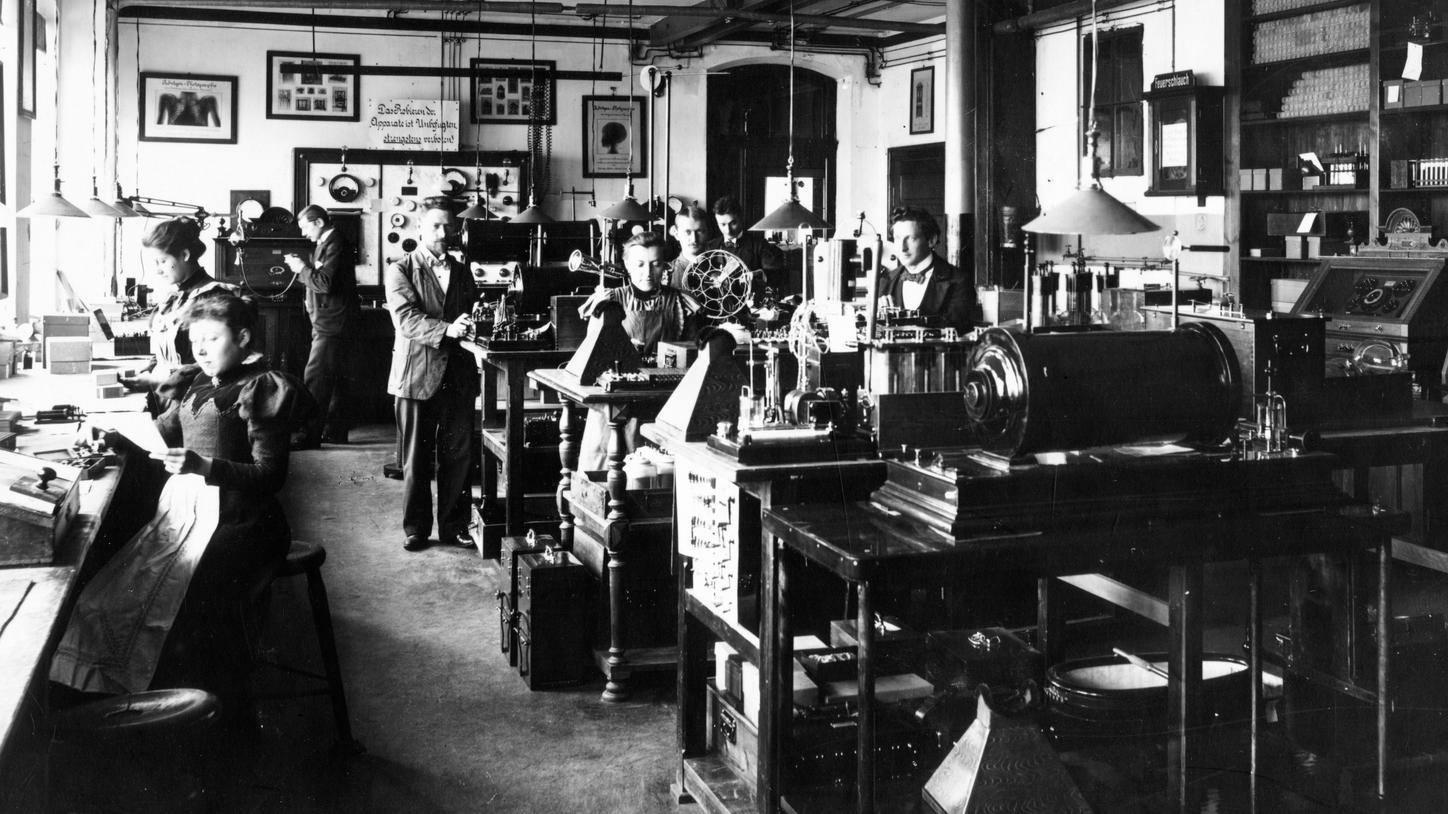
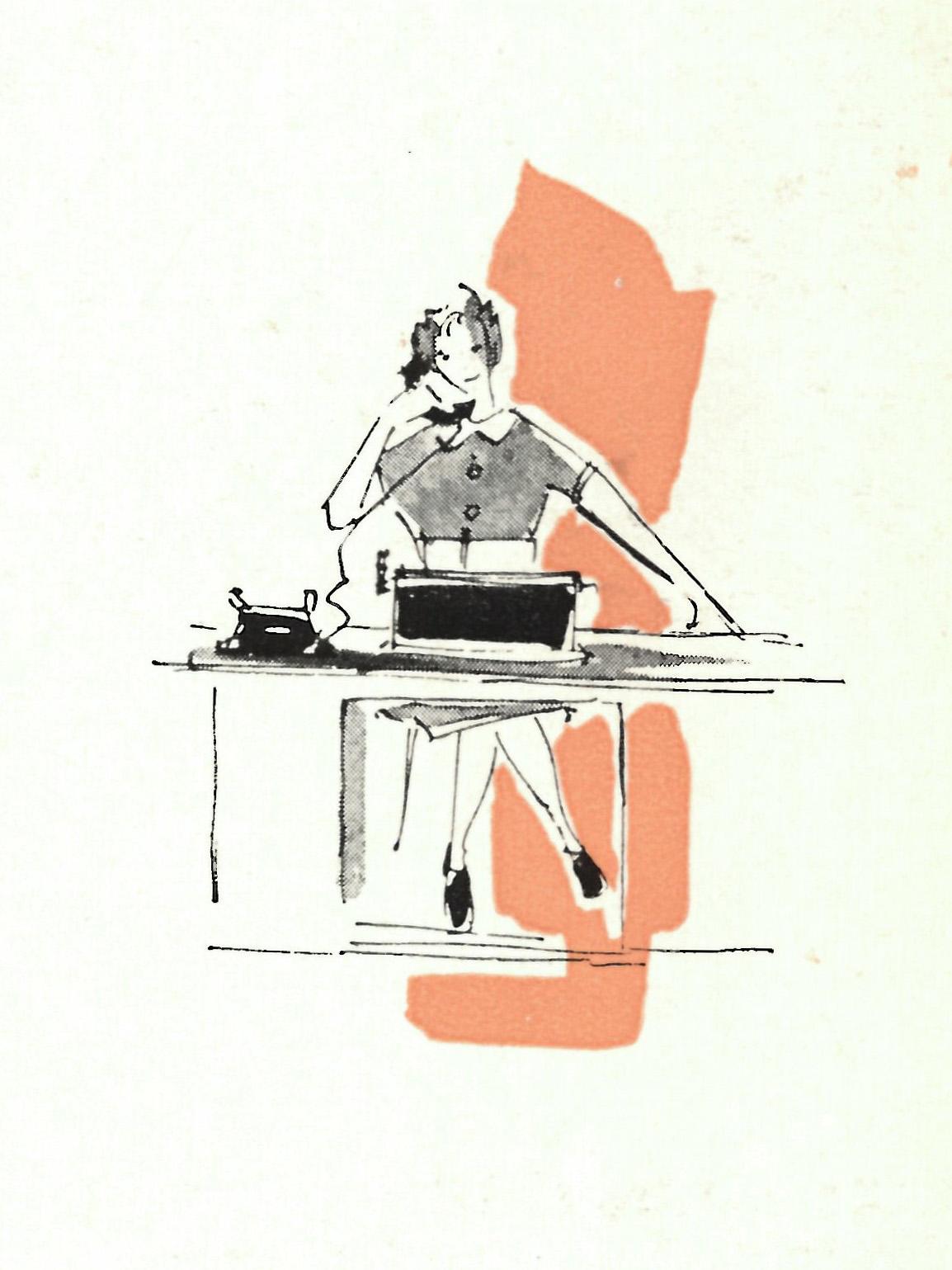
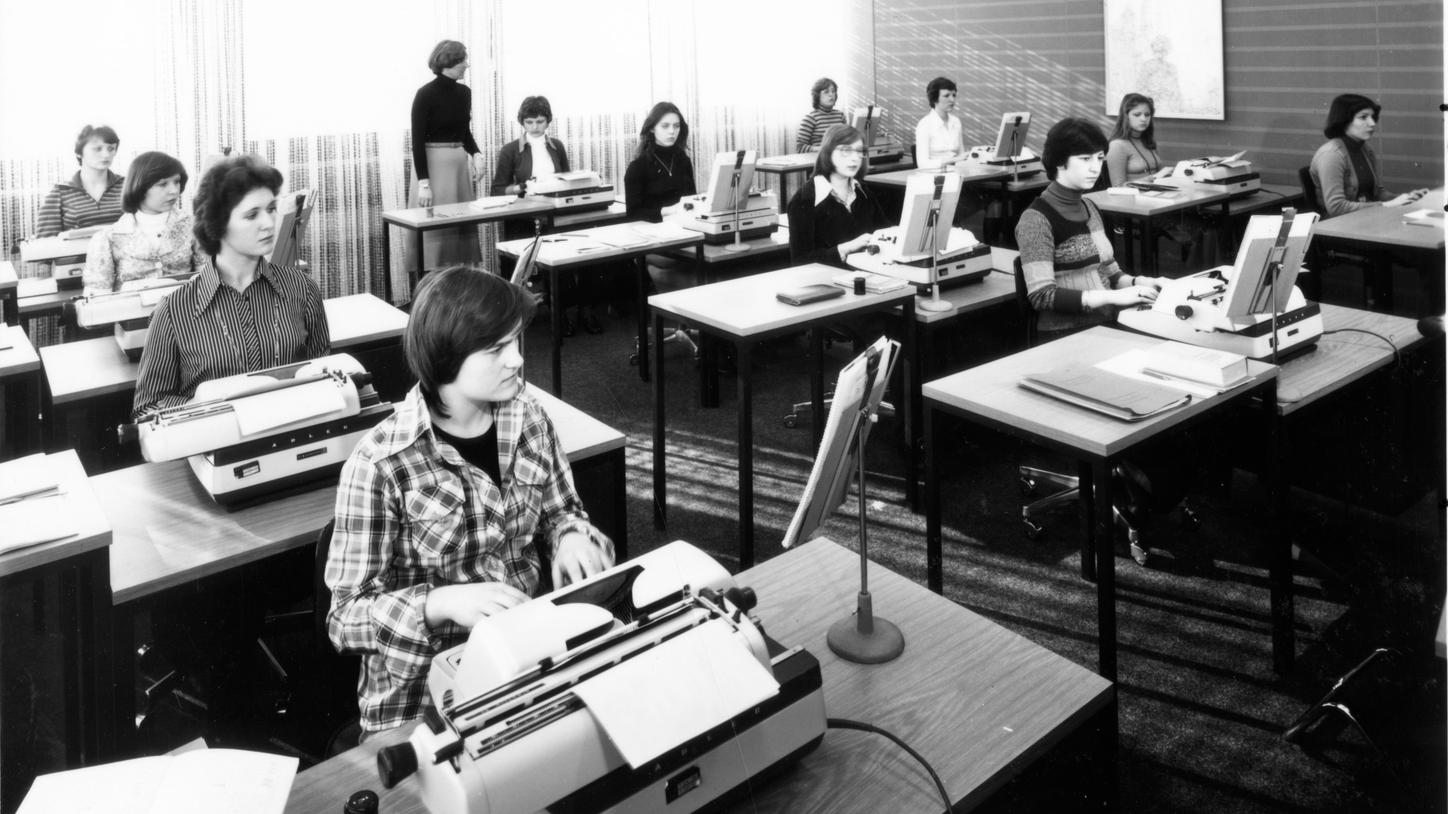
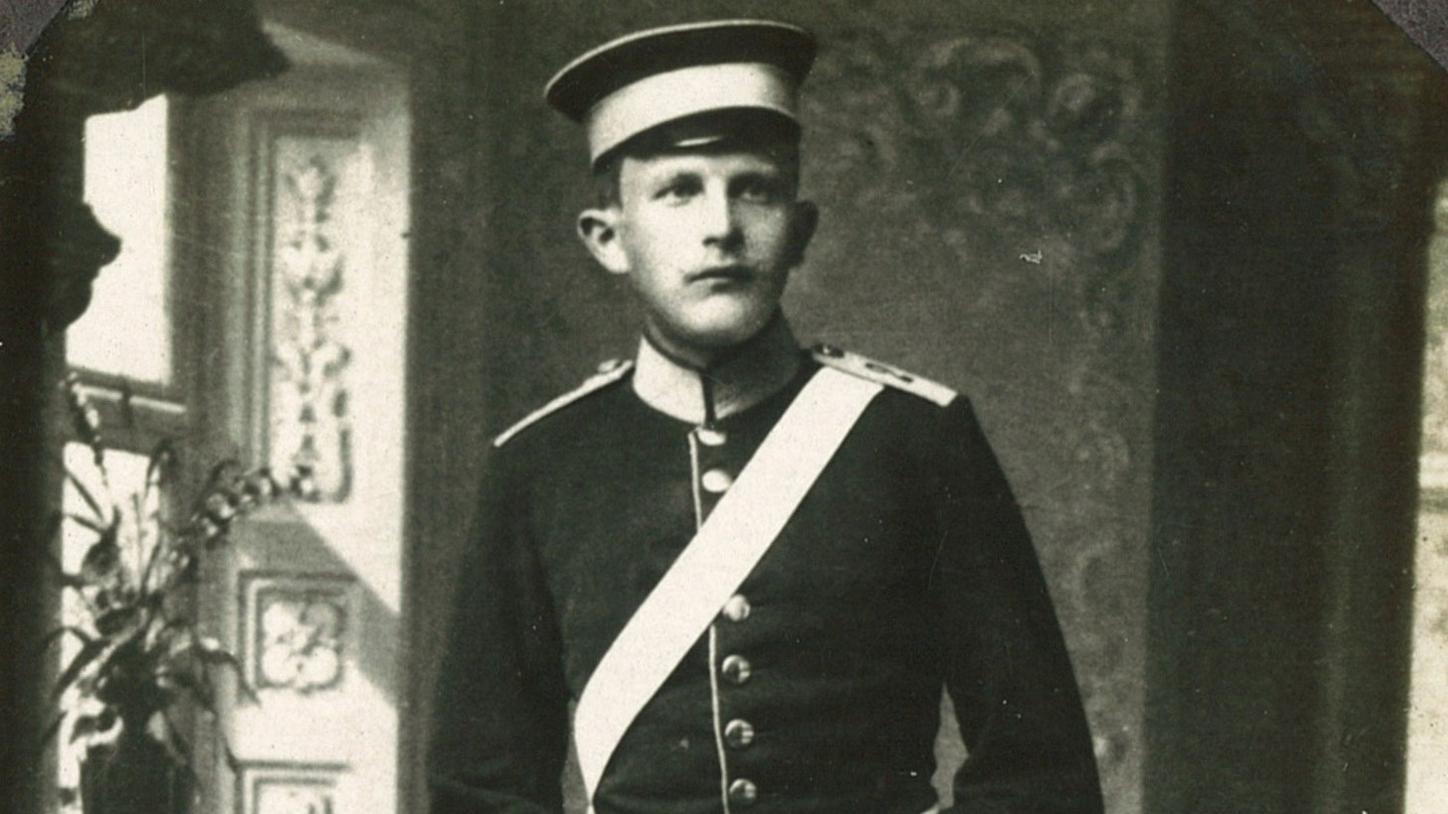
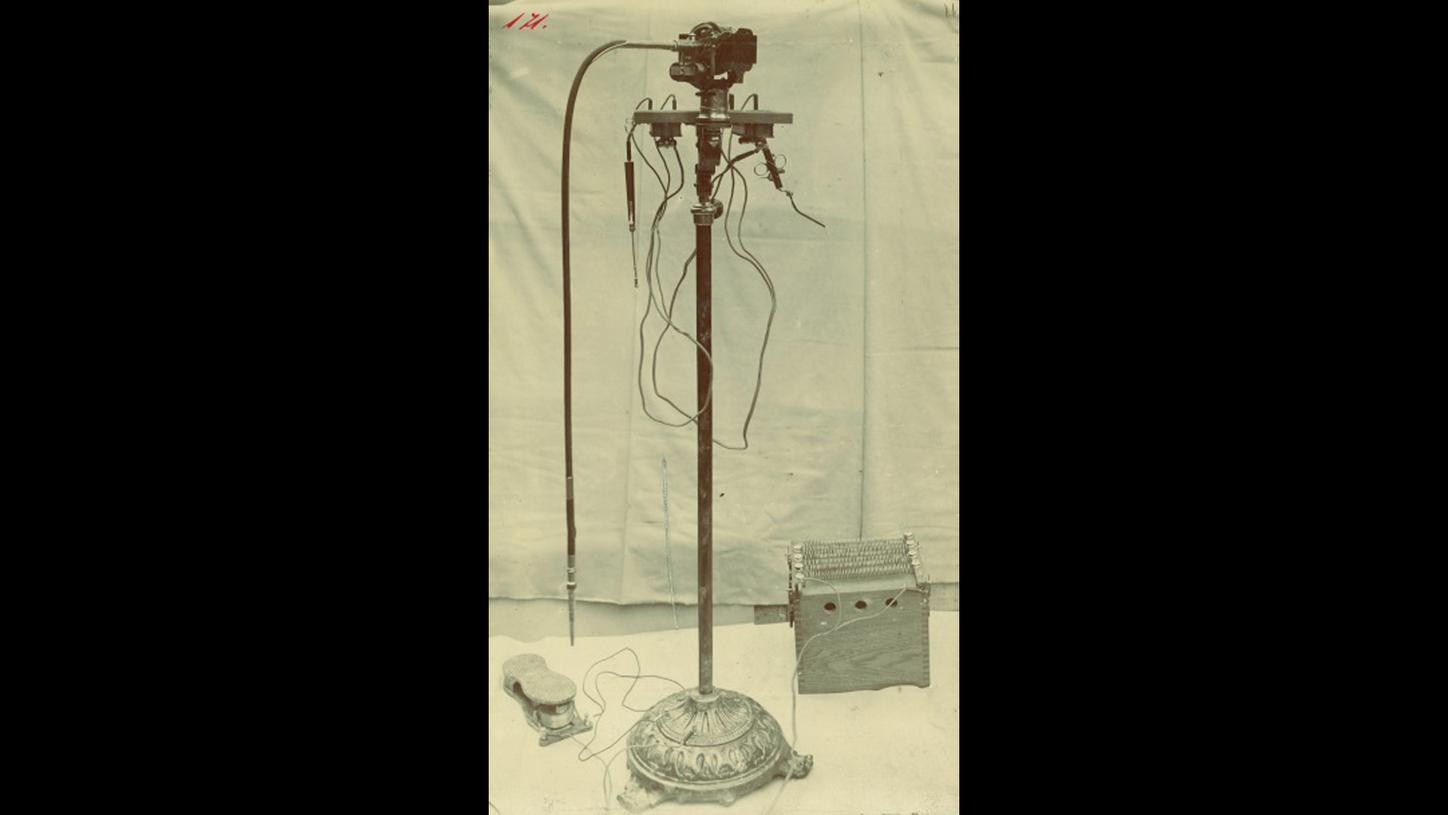

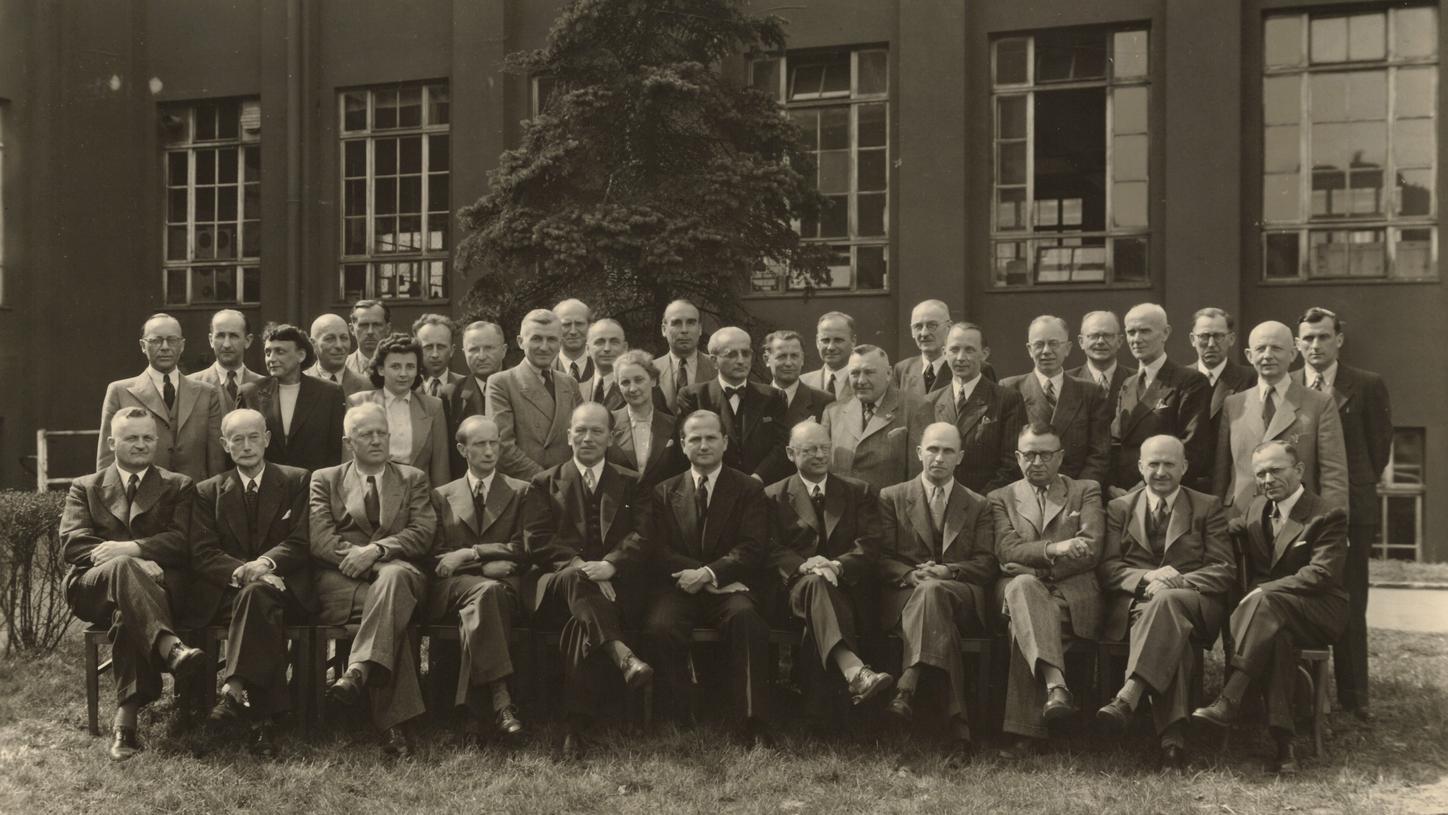
Group photo of the factory managers and the heads of the offices and dental warehouse. Marie Busch is in the middle row, fifth from the left.